The Medical Industry
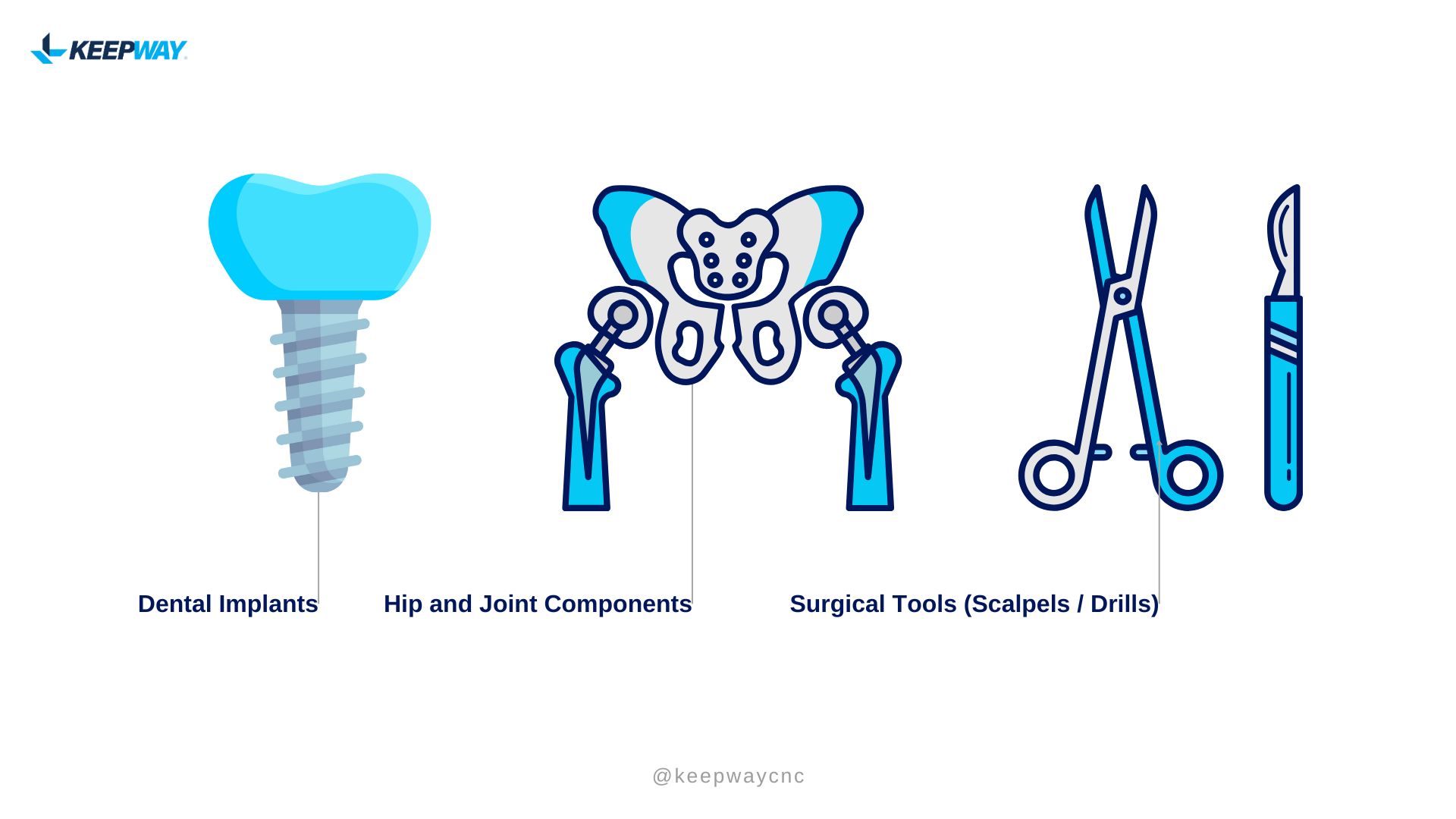
CNC lathes and machining centers play a vital role in the medical industry, where precision, reliability, and biocompatibility are crucial. These machines are used to manufacture a wide variety of medical parts that require tight tolerances, complex geometries, and high-quality finishes. Here’s how CNC lathes and machining centers are applied in the production of medical parts:
Turning Center (CNC lathes)
Orthopedic Implants:
- Bone Screws and Pins:
- Used in fracture fixation procedures.
- Require precise threading and dimensions to ensure proper fit and stability.
- Hip and Joint Components:
- Femoral heads and stems with precise spherical and tapered surfaces.
- Ensure smooth articulation and long-term durability.
- Spinal Implants:
- Rods and connectors used in spinal fusion surgeries.
- Demand exact dimensions and smooth finishes to prevent tissue irritation.
Dental Implants and Components:
- Implant Posts and Abutments:
- Require precise threading and surface smoothness for successful osseointegration.
- Orthodontic Screws and Appliances:
- Custom-fitted components to correct dental alignment issues.
Surgical Instruments:
- Handles and Shafts:
- For tools like scalpels, drills, and reamers.
- Must be ergonomically designed and precisely machined for optimal performance.
- Cannulas and Tubes:
- Used in various surgical procedures for fluid transfer or endoscopy.
- Require exact internal and external diameters and high surface quality.
Prosthetics Components:
- Limb Connectors and Joints:
- Cylindrical parts that allow movement and support in prosthetic limbs.
- Demand high strength and precise tolerances for patient comfort and functionality.
Medical Device Components:
- Valve Bodies and Connectors:
- Used in devices like infusion pumps and dialysis machines.
- Require leak-proof precision and biocompatibility.
The Advantages
- High Precision and Repeatability: Ensures consistent quality across large production runs.
- Excellent Surface Finishes: Critical for implants and instruments to reduce friction and prevent bacterial growth.
- Material Versatility: Capable of machining biocompatible materials such as titanium, stainless steel, and medical-grade plastics.
- Efficiency: Rapid production speeds while maintaining strict tolerances.
- Customization: Easily adaptable for producing custom-sized components for specific patient needs.
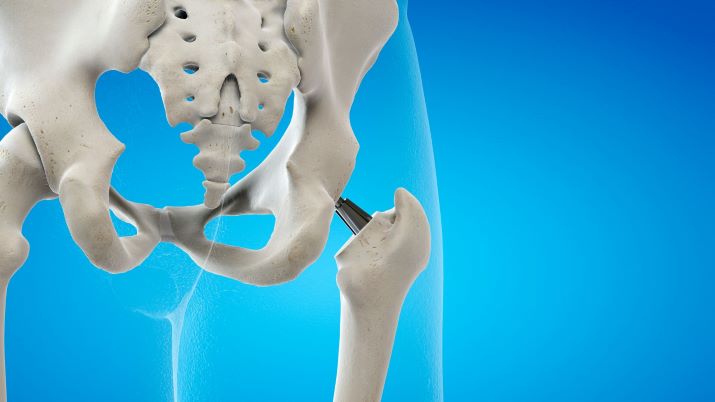
Machining Center
Complex Orthopedic Implants:
- Knee and Shoulder Joint Components:
- Complex geometries requiring multi-axis milling for accurate articulation surfaces.
- Bone Plates and Fixators:
- Customized shapes conforming to patient-specific anatomy.
- Include precise hole placements for screw insertion.
Surgical Instruments and Tools:
- Forceps, Clamps, and Retractors:
- Intricate shapes and precise edges for effective surgical performance.
- Surgical Robotics Components:
- High-precision parts for robotic-assisted surgical systems.
- Demand exceptional accuracy and reliability.
Medical Device Housings and Enclosures:
- Diagnostic Equipment Casings:
- For devices like MRI machines, ultrasound equipment, and monitors.
- Require precise dimensions and high-quality finishes for both functionality and aesthetics.
- Portable Medical Device Components:
- Includes enclosures for devices like insulin pumps and heart monitors.
- Must be durable, lightweight, and ergonomically designed.
Dental Prosthetics and Appliances:
- Crowns, Bridges, and Inlays:
- Custom-crafted to match patient-specific dental structures.
- Require intricate detailing and smooth surfaces.
- Orthodontic Aligners and Retainers:
- Precision milling ensures correct fit and effective treatment outcomes.
Implantable Medical Devices:
- Pacemaker and Neurostimulator Components:
- Small, complex parts with strict tolerances and high reliability requirements.
- Cochlear Implants:
- Require precise machining for effective auditory performance and patient comfort.
The Advantages
- Multi-Axis Machining Capability: Enables the creation of complex geometries and intricate designs in a single setup.
- High Precision and Accuracy: Meets the stringent dimensional and tolerance requirements of medical applications.
- Superior Surface Quality: Essential for reducing infection risks and improving device integration with biological tissues.
- Material Flexibility: Efficiently processes a wide range of materials including alloys, ceramics, and advanced polymers.
- Prototyping and Production Scalability: Suitable for both rapid prototyping of new designs and mass production.
- Reduced Lead Times: Streamlined processes result in faster turnaround from design to finished product.